催化氢化反应在石油化工、精细化工、药物合成等众多领域都具有重要的应用价值,能够将不饱和化合物转化为饱和化合物,提高产品的稳定性、纯度和反应选择性。催化氢化反应装置的设计与优化直接影响着反应的效率、产品质量以及生产成本。
一、催化氢化反应装置的设计原则
(一)反应釜的结构设计
反应釜是催化氢化反应的核心部件,其结构设计应考虑反应的特点和要求。常见的反应釜结构有搅拌式反应釜和固定床反应釜等。搅拌式反应釜适用于液相催化氢化反应,通过搅拌使反应物与催化剂充分混合;固定床反应釜则适用于气相催化氢化反应,反应物在催化剂床层中通过,反应更均匀稳定。
(二)催化剂的装载与分布
催化剂的选择和装载方式对反应效果有影响。不同的反应需要选择合适的催化剂种类、尺寸和形状。在装载催化剂时,要确保催化剂在反应釜内的均匀分布,以提高反应的选择性和转化率。可以采用分级装载、填充助剂等方式来改善催化剂的分布性能,同时要注意防止催化剂颗粒在反应过程中发生团聚或沉降。
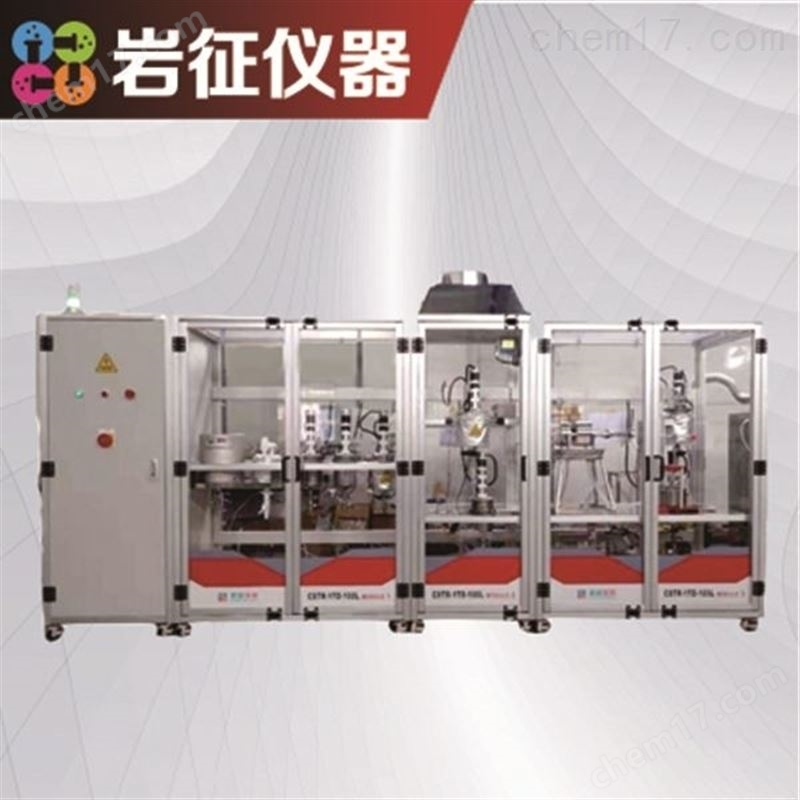
二、优化方法
(一)反应条件的优化
温度控制:温度是影响催化氢化反应速率和选择性的重要因素之一。通过实验研究和模拟计算,确定反应的较佳温度范围。因此,需要根据反应的具体情况,通过温度控制系统精确控制反应温度。
压力调节:氢气压力对反应的进行也起着重要作用。增加氢气压力可以提高氢气在反应物中的溶解度,加快反应速率。但过高的压力也会带来安全风险和设备成本的增加。因此,需要通过调整氢气供应系统的压力和流量,确保氢气压力在合适的范围内。
反应物浓度:合理控制反应物的浓度可以影响反应的转化率和选择性。对于一些高反应活性的反应物,可以适当降低其初始浓度,以减少副反应的发生。同时,要注意反应物之间的比例对反应的影响,使反应物浓度保持在能够促进反应顺利进行且避免副反应的较佳范围内。
(二)催化剂的改性与优化
表面修饰:通过改变催化剂的表面性质,可以提高其活性和选择性。可以采用化学吸附、共沉淀等方法对催化剂进行表面修饰。
负载型催化剂的优化:负载型催化剂在实际应用中具有更好的稳定性和重复使用性能。通过选择合适的载体和负载方式,可以优化催化剂的性能。
(三)装置的操作与控制优化
自动控制系统的应用:采用自动控制系统可以实现对反应过程的自动化控制,提高反应的稳定性和重复性。自动控制系统可以根据反应的实时数据,自动调整温度、压力、流量等反应条件,保证反应在较佳条件下进行。
反应过程的监测与反馈:在反应过程中,实时监测反应的关键参数,通过反馈机制将这些数据传输给控制系统,控制系统根据反馈信息及时调整反应条件,使反应过程始终保持在较佳状态。
催化氢化反应装置的设计与优化是一个复杂而系统的工程,需要综合考虑反应的特点和要求,从反应釜的结构设计、催化剂的装载与分布、反应条件的优化以及装置的操作与控制等多个方面进行优化。通过合理的设计和优化方法,可以提高催化氢化反应的效率和质量,为相关领域的生产和发展提供有力的技术支持。
免责声明
- 凡本网注明“来源:化工仪器网”的所有作品,均为浙江兴旺宝明通网络有限公司-化工仪器网合法拥有版权或有权使用的作品,未经本网授权不得转载、摘编或利用其它方式使用上述作品。已经本网授权使用作品的,应在授权范围内使用,并注明“来源:化工仪器网”。违反上述声明者,本网将追究其相关法律责任。
- 本网转载并注明自其他来源(非化工仪器网)的作品,目的在于传递更多信息,并不代表本网赞同其观点和对其真实性负责,不承担此类作品侵权行为的直接责任及连带责任。其他媒体、网站或个人从本网转载时,必须保留本网注明的作品第一来源,并自负版权等法律责任。
- 如涉及作品内容、版权等问题,请在作品发表之日起一周内与本网联系,否则视为放弃相关权利。